Comment concevoir des pièces en plastique
Brève description:
À conception de pièces en plastiqueconsiste à définir la forme, la taille et la précision des pièces, en fonction du rôle que jouent les pièces dans le produit, et la règle du processus de moulage du plastique. Le résultat final est des dessins pour la fabrication du moule et de la pièce en plastique.
La fabrication du produit commence par la conception. La conception des pièces en plastique détermine directement la réalisation de la structure interne, le coût et la fonction du produit, et détermine également l'étape suivante de la production du moule, le coût et le cycle, ainsi que le processus et le coût de moulage par injection et de post-traitement.
Les pièces en plastique sont largement utilisées dans divers produits, installations et la vie des gens dans la société moderne. Les pièces en plastique nécessitent différentes formes et fonctions. Ils utilisent des matières plastiques et leurs propriétés sont variées. Dans le même temps, il existe de nombreuses façons de fabriquer des pièces en plastique dans l'industrie. Ainsi, concevoir des pièces en plastique n'est pas un travail simple.
La conception et le matériau différents des pièces sont produits par un traitement différent. Le traitement pour le moulage du plastique comprend principalement ci-dessous:
1. moulage par injection
2. moulage par soufflage
3. moulage par compression
4. moulage par rotation
5. thermoformage
6. extrusion
7. fabrication
8. mousse
Il existe de nombreuses façons de les produire en masse. Le moulage par injection est une méthode de fabrication populaire, car les pièces en plastique moulées par injection à 50% ~ 60% sont produites par moulage par injection, il s'agit d'une capacité de production à grande vitesse.
Vitrine de certaines pièces en plastique que nous avons conçues:
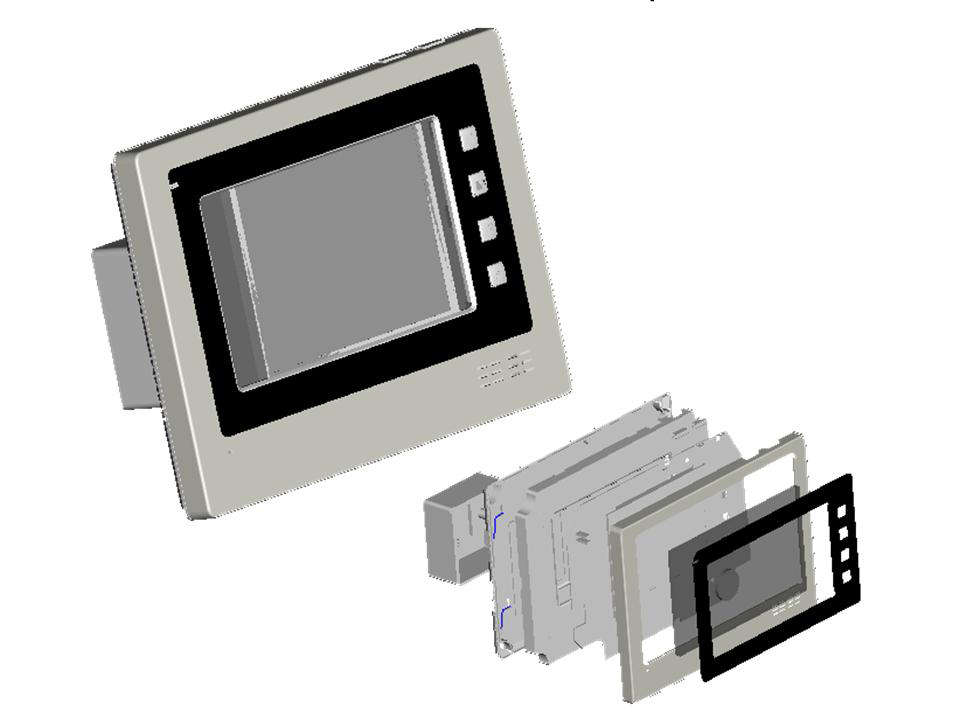
Boîtier en plastique du téléphone vision
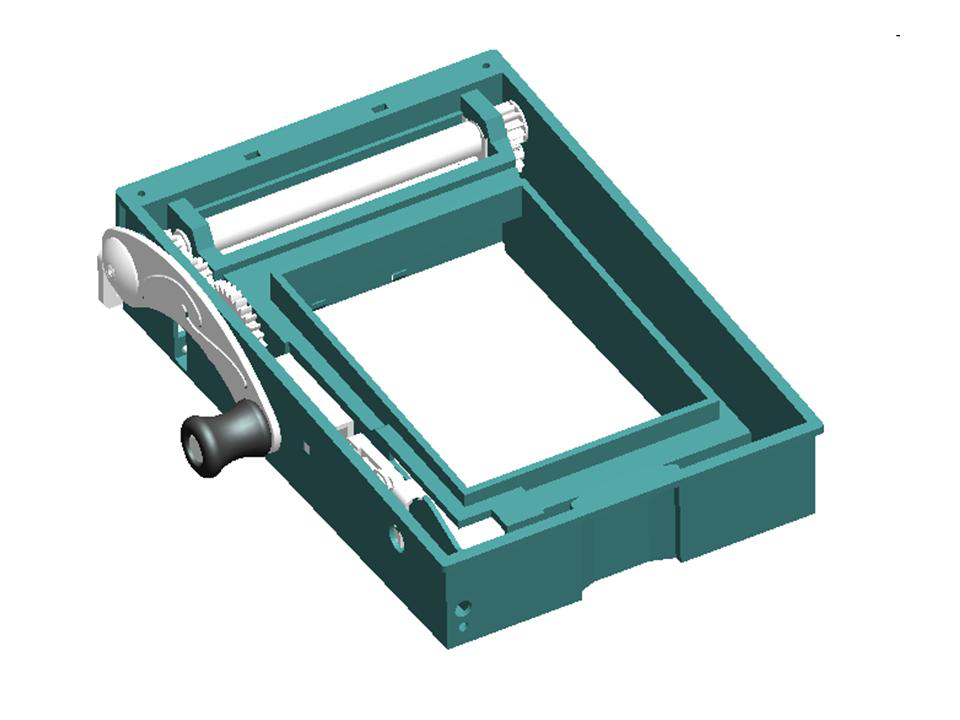
Pièces en plastique du mécanisme
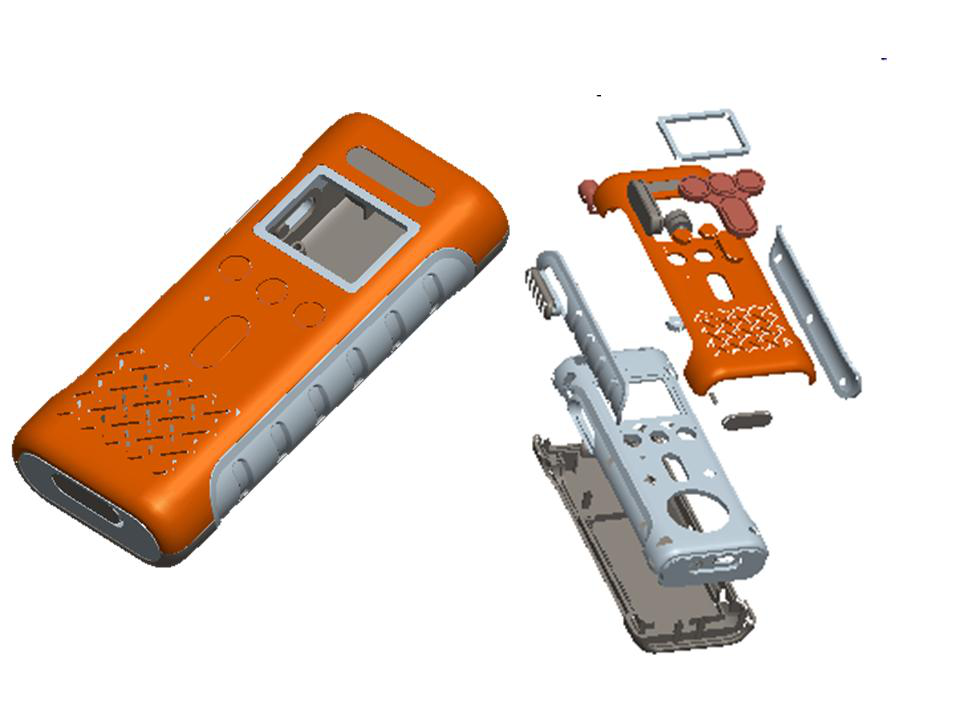
Boîtiers en plastique d'électronique
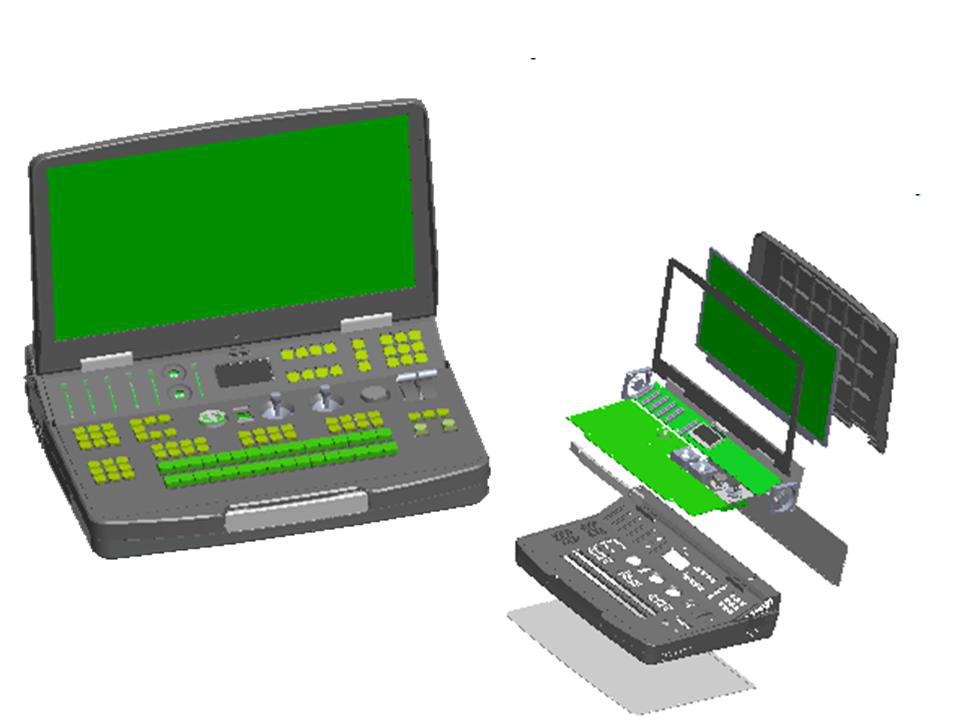
Boîtier en plastique pour instrument
Ci-dessous, nous partageons des détails sur la conception de pièces en plastique sous trois aspects
* 10 conseils pour concevoir des pièces en plastique que vous devez connaître
1.Déterminez la conception de l'apparence et la taille du produit.
C'est la première étape de tout le processus de conception. Selon les études de marché et les exigences des clients, déterminez l'apparence et la fonction des produits et formulez les tâches de développement de produits.
Selon la tâche de développement, l'équipe de développement poursuit l'analyse de faisabilité technique et technologique du produit et construit le modèle d'apparence 3D du produit. Ensuite, en fonction de la réalisation des fonctions et de l'assemblage du produit, des pièces éventuelles sont prévues.
2.Séparez les pièces individuelles des dessins de produits, choisissez le type de résine plastique pour les pièces en plastique
Cette étape consiste à séparer les pièces du modèle 3D obtenu à l'étape précédente et à les concevoir individuellement. Selon les exigences fonctionnelles des pièces, choisissez des matières premières plastiques ou des matériaux de quincaillerie appropriés. Par exemple, l'ABS est généralement utilisé dans le
coque, ABS / BC ou PC doit avoir certaines propriétés mécaniques, des pièces transparentes telles que l'abat-jour, un lampadaire PMMA ou PC, des pièces d'équipement ou d'usure POM ou Nylon.
Après avoir sélectionné le matériau des pièces, la conception détaillée peut être lancée.
3.Définir les angles de dépouille
Les angles de dépouille permettent de retirer le plastique du moule. Sans angles de dépouille, la pièce offrirait une résistance significative due au frottement lors du retrait. Les angles de dépouille doivent être présents à l'intérieur et à l'extérieur de la pièce. Plus la pièce est profonde, plus l'angle de dépouille est grand. Une règle de base simple est d'avoir un angle de dépouille de 1 degré par pouce. Un angle de dépouille insuffisant peut entraîner des éraflures sur les côtés de la pièce et / ou de grandes marques de goupille d'éjection (nous en parlerons plus tard).
Angles de dépouille de la surface extérieure: plus la pièce est profonde, plus l'angle de dépouille est grand. Une règle de base simple est d'avoir un angle de dépouille de 1 degré par pouce. Un angle de dépouille insuffisant peut entraîner des éraflures sur les côtés de la pièce et / ou de grandes marques de goupille d'éjection (nous en parlerons plus tard).
Habituellement, pour avoir un bon aspect de la surface, la texture est faite à la surface des pièces. Le mur texturé est rugueux, le frottement est important et il n'est pas facile de le retirer de la cavité, il nécessite donc un angle de dessin plus grand. La texture la plus grossière est le plus grand angle de dessin nécessaire.
4.Définir l'épaisseur de la paroi / épaisseur uniforme
Le moulage de forme solide n'est pas souhaité dans le moulage par injection pour les raisons suivantes:
1) .Le temps de refroidissement est proportionnel au carré de l'épaisseur de la paroi. Un long temps de refroidissement pour le solide vaincra l'économie de la production de masse. (mauvais conducteur de chaleur)
2) .Les sections plus épaisses rétrécissent plus que les sections plus minces, introduisant ainsi un retrait différentiel entraînant un gauchissement ou une marque d'évier, etc.
Par conséquent, nous avons une règle de base pour la conception de pièces en plastique; dans la mesure du possible, l'épaisseur de la paroi doit être uniforme ou constante dans toute la pièce. Cette épaisseur de paroi est appelée épaisseur de paroi nominale.
S'il y a une section pleine dans la pièce, elle doit être creuse en introduisant un noyau. Cela devrait garantir une épaisseur de paroi uniforme autour du noyau.
3) .Quelles sont les considérations pour décider de l'épaisseur de la paroi?
Il doit être suffisamment épais et rigide pour le travail. L'épaisseur de la paroi peut être de 0,5 à 5 mm.
Il doit également être suffisamment fin pour refroidir plus rapidement, ce qui réduit le poids des pièces et augmente la productivité.
Toute variation d'épaisseur de paroi doit être maintenue au minimum.
Une pièce en plastique avec une épaisseur de paroi variable connaîtra des taux de refroidissement et des rétrécissements différents. Dans ce cas, il devient très difficile et souvent impossible d'atteindre une tolérance étroite. Lorsque la variation d'épaisseur de paroi est essentielle, la transition entre les deux doit être progressive.
5. conception de connexion entre les pièces
Habituellement, nous devons connecter deux coques ensemble. Pour former une pièce fermée entre eux pour placer les composants internes (assemblage ou mécanisme PCB).
Les types de connexion habituels:
1). Mousquetons:
La connexion par mousquetons est couramment utilisée dans les produits de petite et moyenne taille. Sa caractéristique est que les mousquetons sont généralement fixés au bord des pièces et que la taille du produit peut être réduite. Une fois assemblé, il est fermé directement sans utiliser d'outils tels que tournevis, matrice de soudage par ultrasons et autres. L'inconvénient est que les mousquetons peuvent rendre la moisissure plus compliquée. Le mécanisme de glissière et le mécanisme de levage sont nécessaires pour réaliser la connexion des mousquetons et augmenter le coût du moule.
2). Joints à vis:
Les joints à vis sont fermes et fiables. En particulier, la fixation vis + écrou est très fiable et durable, permettant de multiples démontages sans fissures. Le raccordement vissé convient aux produits avec une grande force de verrouillage et des démontages multiples. L'inconvénient est que la colonne à vis prend plus de place.
3). Bosses de montage:
La connexion des bossages de montage consiste à fixer deux pièces par la coordination étroite entre les bossages et les trous. Ce mode de connexion n'est pas assez solide pour permettre le démontage des produits. L'inconvénient est que la force de verrouillage diminue à mesure que le temps de démontage augmente.
4). Soudage par ultrasons:
Le soudage par ultrasons consiste à placer les deux pièces dans le moule à ultrasons et à fusionner la surface de contact sous l'action d'une machine de soudage par ultrasons. La taille du produit peut être plus petite, le moule d'injection est relativement simple et la connexion est ferme. L'inconvénient est l'utilisation d'un moule à ultrasons et d'une machine de soudage par ultrasons, la taille du produit ne peut pas être trop grande. Après le démontage, les pièces à ultrasons ne peuvent plus être utilisées.
6. contre-dépouilles
Les contre-dépouilles sont des éléments qui interfèrent avec le retrait de l'une ou l'autre moitié du moule. Les contre-dépouilles peuvent apparaître à peu près n'importe où dans la conception. Celles-ci sont tout aussi inacceptables, sinon pires que l'absence d'angle de dépouille sur la pièce. Cependant, certaines contre-dépouilles sont nécessaires et / ou inévitables. Dans ces cas, nécessaire
les contre-dépouilles sont produites par des pièces coulissantes / mobiles dans le moule.
Gardez à l'esprit que la création de contre-dépouilles est plus coûteuse lors de la production du moule et doit être réduite au minimum.
7. soutien côtes / goussets
Les nervures dans la pièce en plastique améliorent la rigidité (relation entre la charge et la flèche de la pièce) de la pièce et augmentent la rigidité. Il améliore également la capacité de moulage car ils accélèrent l'écoulement de la matière fondue dans le sens de la nervure.
Les nervures sont placées le long de la direction de la contrainte maximale et de la déflexion sur les surfaces non apparentes de la pièce. Le remplissage, le retrait et l'éjection du moule doivent également influencer les décisions de placement des nervures.
Les côtes qui ne se joignent pas à la paroi verticale ne doivent pas se terminer brusquement. Une transition progressive vers le mur nominal devrait réduire le risque de concentration de contraintes.
Côte - dimensions
Les côtes doivent avoir les dimensions suivantes.
L'épaisseur de la nervure doit être comprise entre 0,5 et 0,6 fois l'épaisseur nominale de la paroi pour éviter les traces de creux.
La hauteur des nervures doit être de 2,5 à 3 fois l'épaisseur nominale de la paroi.
La nervure doit avoir un angle de dépouille de 0,5 à 1,5 degrés pour faciliter l'éjection.
La base des nervures doit avoir un rayon de 0,25 à 0,4 fois l'épaisseur nominale de la paroi.
La distance entre deux nervures doit être de 2 à 3 fois (ou plus) l'épaisseur de paroi nominale.
8. arêtes rayonnées
Lorsque deux surfaces se rencontrent, cela forme un coin. Au coin, l'épaisseur de la paroi augmente jusqu'à 1,4 fois l'épaisseur de paroi nominale. Il en résulte un retrait différentiel, une contrainte de moulage et un temps de refroidissement plus long. Par conséquent, le risque de panne de service augmente aux angles vifs.
Pour résoudre ce problème, les coins doivent être lissés avec un rayon. Radius doit être fourni aussi bien en externe qu'en interne. Ne jamais avoir de coin pointu interne car il favorise la fissuration. Le rayon doit être tel qu'il confirme la règle d'épaisseur de paroi constante. Il est préférable d'avoir un rayon de 0,6 à 0,75 fois l'épaisseur de paroi aux coins. Ne jamais avoir de coin pointu interne car il favorise la fissuration.
9. conception de bossage à vis
Nous utilisons toujours des vis pour fixer deux demi-boîtiers ensemble, ou pour fixer le PCBA ou d'autres composants sur les pièces en plastique. Les bossages de vis sont donc la structure pour le vissage et les pièces fixes.
Le bossage de la vis est de forme cylindrique. Le bossage peut être lié à la base avec la partie mère ou il peut être lié sur le côté. La liaison sur le côté peut entraîner une section épaisse de plastique, ce qui n'est pas souhaitable car cela peut provoquer une marque de coulage et augmenter le temps de refroidissement. Ce problème peut être résolu en liant le bossage à travers une nervure à la paroi latérale comme indiqué dans l'esquisse. Le bossage peut être rendu rigide en fournissant des nervures de renfort.
La vis est utilisée sur le bossage pour fixer une autre partie. Il existe des vis de type filetage et des vis à coupe de bande de roulement. Les vis de formation de filetage sont utilisées sur les thermoplastiques et les vis de filetage sont utilisées sur les pièces en plastique thermodurcissables inélastiques.
Les vis formant filetage produisent des filetages femelles sur la paroi interne du bossage par écoulement à froid - le plastique est localement déformé plutôt que coupé.
Le bossage de la vis doit avoir des dimensions appropriées pour résister aux forces d'insertion des vis et à la charge exercée sur la vis en service.
La taille de l'alésage par rapport à la vis est critique pour la résistance au dénudage du filetage et à l'arrachement de la vis.
Le diamètre extérieur du bossage doit être suffisamment grand pour résister aux contraintes de cercle dues à la formation du filetage.
L'alésage a un diamètre légèrement plus grand au niveau de l'évidement d'entrée pour une courte longueur. Cela aide à localiser la vis avant l'enfoncement. Cela réduit également les contraintes à l'extrémité ouverte du bossage.
Les fabricants de polymères donnent des directives pour déterminer la dimension du bossage pour leurs matériaux. Les fabricants de vis donnent également des directives sur la bonne taille d'alésage pour la vis.
Des précautions doivent être prises pour assurer des joints de soudure solides autour de l'alésage de la vis dans le bossage.
Des précautions doivent être prises pour éviter le stress moulé chez le patron, car il peut échouer dans un environnement agressif.
L'alésage dans le bossage doit être plus profond que la profondeur du filetage.
10. décoration de surface
Parfois, afin d'obtenir une belle apparence, nous effectuons souvent un traitement spécial sur la surface du boîtier en plastique.
Tels que: texture, haute brillance, peinture au pistolet, gravure au laser, estampage à chaud, galvanoplastie et ainsi de suite. Il est nécessaire de prendre en compte à l'avance dans la conception du produit, pour éviter que le traitement ultérieur ne puisse être réalisé ou que les changements de taille affectent l'assemblage du produit.